Exploring the World of Plastic Injection Molding Products
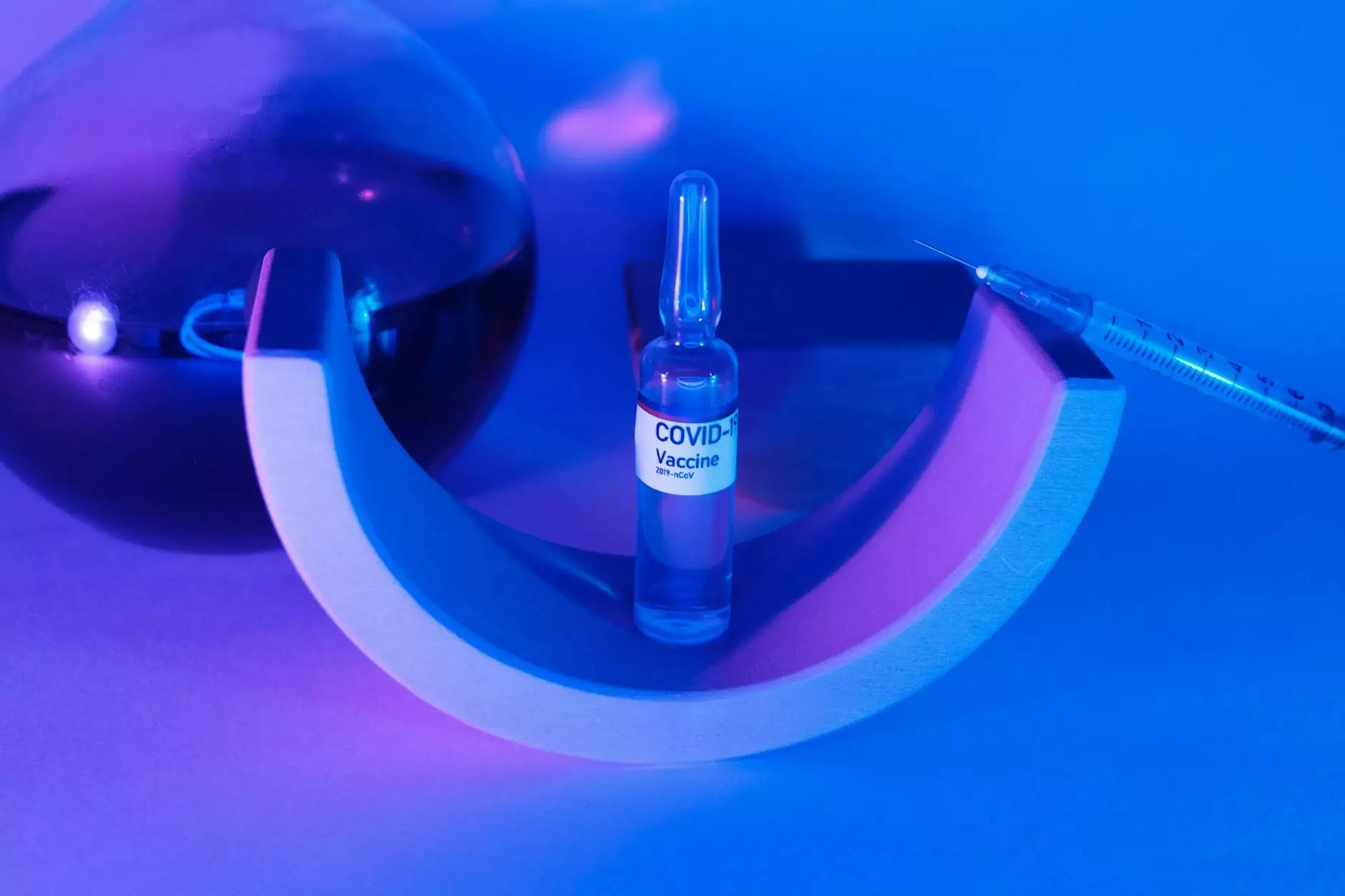
Plastic injection molding is one of the most prevalent manufacturing processes used today. It involves the production of plastic parts by injecting molten plastic into a mold. This exciting and efficient technique has revolutionized the manufacturing industry, catering to a wide array of applications ranging from electronics components to automotive parts. In this article, we will delve into the importance of plastic injection molding products, their production process, applications, and how they contribute to diverse industries.
What is Plastic Injection Molding?
Plastic injection molding is a versatile manufacturing process that allows for the creation of complex shapes and designs. This method contributes significantly to producing high-quality plastic parts efficiently and cost-effectively. The process involves several key steps:
- Material Selection: The first step in the injection molding process is selecting the appropriate plastic material. Common materials include acrylonitrile butadiene styrene (ABS), polycarbonate (PC), and polyethylene (PE).
- Mold Design: After selecting the material, a mold is created. The mold is often made of steel or aluminum and is designed to meet the specific needs of the products being produced.
- Injection: The plastic resin is heated until it becomes molten and is then injected into the mold under pressure.
- Cooling: The injected plastic is allowed to cool and solidify inside the mold.
- Demolding: Once the part has cooled, it is removed from the mold, often with the use of automated machinery.
The Advantages of Plastic Injection Molding Products
Plastic injection molding products offer numerous advantages, making them a preferred choice in various industries. Some of these advantages include:
- High Production Efficiency: Once the mold is created, thousands of identical parts can be produced rapidly, significantly speeding up the manufacturing process.
- Complex Geometries: This process allows for intricate designs that may be impossible or too costly to achieve with other manufacturing techniques.
- Material Versatility: A wide range of plastic materials can be used, allowing manufacturers to select the one that best fits their product's requirements.
- Cost-Effectiveness: With high production rates, the cost per unit decreases, making it an economically viable option for mass production.
- Quality and Precision: Injection molding can produce parts with tight tolerances, ensuring high-quality products are delivered consistently.
Applications of Plastic Injection Molding Products
The applications of plastic injection molding products are vast and varied. Here are some key industries that benefit from this technology:
1. Automotive Industry
In the automotive sector, injection molding is used to create a wide variety of components, including:
- Dashboard panels
- Car door handles
- Headlight housings
- Automotive interior trims
These products must meet strict durability and aesthetic standards, and injection molding provides the necessary precision and reliability.
2. Medical Devices
Medical devices utilize plastic injection molding products due to their ability to produce complex shapes. Common applications include:
- Syringe bodies
- Drug delivery devices
- Diagnostic equipment housings
- Implantable devices
The medical industry requires stringent hygiene and safety standards, and injection molding allows manufacturers to meet these requirements efficiently.
3. Consumer Electronics
The consumer electronics industry relies on injection-molded parts for various devices. Applications include:
- Smartphone casings
- Laptop components
- Remote controls
The aesthetic and functional requirements of electronics make injection molding an ideal manufacturing technique.
4. Packaging
Effective packaging solutions often require precision-molded components, such as:
- Bottles and containers
- Caps and closures
- Packaging trays
In this context, injection molding contributes to both the functionality and the visual appeal of products.
The Future of Plastic Injection Molding Products
As technology continues to evolve, the future of plastic injection molding products looks promising. Some anticipated developments include:
1. Sustainability in Materials
With the increasing importance of sustainability, manufacturers are exploring bio-based and recyclable materials for injection molding. This shift aims to reduce the environmental impact of plastic production.
2. Advanced Manufacturing Techniques
Integrating technologies like advanced automation and artificial intelligence will enhance production efficiency and reduce costs. Smart factories may soon leverage these technologies for real-time monitoring and optimization.
3. Customization and Short Runs
As consumer preferences shift towards personalized products, injection molding technology is adapting to allow for smaller production runs with greater variability. This flexibility can cater to niche markets and unique customer demands.
Industry Standards and Quality Control
Ensuring the quality of plastic injection molding products is crucial. Various industry standards guide manufacturing practices, including:
- ISO 9001: A quality management standard that focuses on maintaining an effective quality management system.
- FDA Regulations: Especially important for medical and food-related applications, ensuring products are safe for use.
- UL Certification: Relevant for products that require safety-related certification.
Manufacturers must comply with these standards, adopting rigorous testing procedures to guarantee the quality and safety of their products.
Conclusion
The world of plastic injection molding products is vast, diverse, and continually evolving. From automotive to medical applications, the benefits of using injection molding techniques cannot be overstated. Understanding the processes, advantages, and future trends will empower businesses to leverage this technology effectively.
For companies involved in manufacturing, partnering with experienced providers like Deep Mould (found at deepmould.net) can enhance production capabilities and ensure high-quality products that meet market demands.
Frequently Asked Questions (FAQs)
What are the main materials used in plastic injection molding?
The most commonly used materials are acrylonitrile butadiene styrene (ABS), polycarbonate (PC), and various types of polyethylene (PE).
How does injection molding differ from other manufacturing methods?
Injection molding provides greater precision, allows complex geometries, and is more efficient for mass production compared to methods like machining or 3D printing.
Can injection molding be used for small production runs?
While injection molding is often associated with high-volume production, advancements in technology are enabling smaller production runs with customizable designs.